Home > Technical Blog > 5 common causes of casual food line downtime

5 common causes of casual food line downtime
August 11, 2022Snack food production lines are designed to produce a high volume of product in a short amount of time. The machinery that runs these lines is complex, and breakdowns can occur at any time. When a shutdown occurs, the line must be stopped immediately so that the problem can be identified and repaired.
There are many reasons why snack food production lines shut down unexpectedly. Some cause minor delays while others can cause extensive damage to equipment and product. Here are five common causes for snack food production line shutdowns.
Contamination caused by metal particles.
Metal particles are the most common reason for snack food production line shutdowns. The safety of the food is paramount, and it can be hard to catch contamination before it spreads throughout the entire batch. Even if one piece of metal was able to get through the sorting process, it could ruin hundreds if not thousands of products.
Plastic pieces in snack foods.
Plastic pieces are another common reason for snack food production line shutdowns. These small pieces can be difficult to detect and remove from the product itself, but they can also cause serious injury if ingested by a customer (especially children).
The presence of other contaminants.
While metal particles and plastic pieces are the two most common reasons why snack food production lines shut down, there are many other types of contaminants that can cause issues as well. These may include things like insects or even human hair that somehow made its way into the final product.
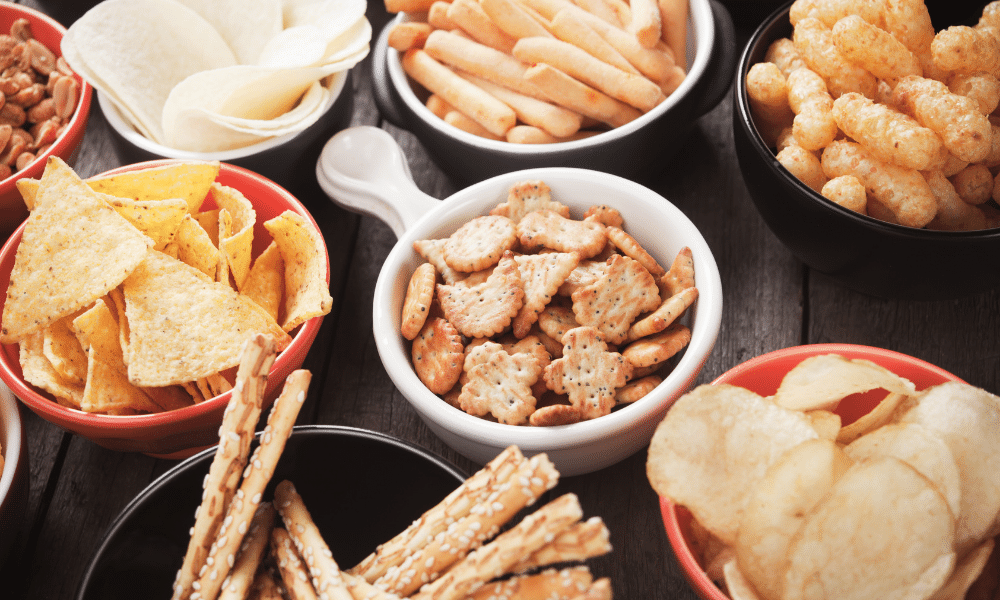
5 Common Causes for Snack Food Production Line Shutdowns
Damaged metal fill.
Metal fill is a common cause of snack food production lines shutdowns. Metal fill is the process of adding metal to the product to reduce shrinkage and increase weight. The metal can be added through a plate filler or a tumbler filler. If done incorrectly, it can cause damage to the equipment and product.
Incorrectly adjusted crumbler. Crumblers are used to break up pieces of filling and make them smaller in size. They also help distribute other ingredients throughout the product like cheese shreds or nuts. If they are not adjusted correctly, they can cause damage to the filling application equipment and product such as jamming or tearing holes in the package film or even damaging the machine itself by pulling parts off it such as screws, bolts, etc.. This can lead to increased downtime due to repairs or replacement of parts or even whole machines if they cannot be repaired quickly enough by your maintenance staff
Product abnormalities caused by improper temperature control; i.e., inconsistencies in product viscosity, agglomeration and extrusion problems.
Inconsistent viscosity (viscosity is the ‘thickness’ of a liquid or a gas) throughout the batch will lead to inconsistent output. A high viscosity can cause clogging of equipment, while a low viscosity will cause the product to flow too freely through the equipment and will not maintain its shape or texture.
Agglomeration occurs when two or more particles stick together during processing. Agglomeration can result in improper texture, color and taste of the finished product.
Extrusion problems are often caused by sudden changes in temperature within the extruder barrel or at the exit end of the barrel. These sudden changes can cause sticking of products within the barrel or on exit ends of extruders, causing shutdowns and loss of production time and money
Spills caused by broken seals or cracked housings on manufacturing equipment, resulting in production downtime and sanitation concerns.
Broken seals and cracked housings on manufacturing equipment are common causes of snack food production line shutdowns. The main reason for this is that the seals and housings are made from a variety of materials. When the material is not strong enough to withstand the pressure of the product being pumped through it, it will break or crack. This often results in a significant amount of product leakage into other areas of the plant, causing not only downtime but also sanitation concerns as well as potential contamination issues.
A major factor in determining whether a seal or housing will be able to withstand the pressures associated with pumping products through it is its design and how much stress it can handle before failing. Many times when there is an issue with one of these parts, it’s due to poor design or inadequate materials used during construction.
Poorly positioned bearings cause chatter, vibration and machine wear; resulting in costly downtime and maintenance, reduced quality and yields, and shorter bearing life expectancy.
Inadequate lubrication is a common cause of bearing failure and shutdowns. Lubricating grease should be applied to the bearing to ensure proper operation. The temperature of the grease must be above the operating temperature of the bearing. If the lubrication is too thick or under-filled, it will plug up the bearing and reduce its efficiency as well as lead to premature failure.
Improper belt tensioning can cause damage to bearings when they become loose in their housings or spin out of position. When belts are tightened improperly, they can cause undue stress on the bearings causing premature wear or failure. Proper belt tensioning will help prevent this type of damage from happening again.
Check out these common causes of snack food production line shutdowns to see if you can avoid them or avoid them increasing their impact on your business if they do occur
The snack food production line is a critical part of your business. It helps you turn raw ingredients into finished products that can be sold to customers, providing a steady stream of income for your company.
Unfortunately, snack food production lines do sometimes experience problems. You may need to shut down the line for maintenance or repair work or because of an equipment failure.
When this happens, it's important to know how to keep the downtime as short as possible so that you don't lose any potential sales opportunities or damage customer relationships.
Identifying the proper cause for a downtime on your production line is critical to fixing the problem, as this will help determine what type of maintenance or repairs are required to correct the issue. If you need assistance identifying where something went wrong, an operations engineer can help. An experienced turnaround specialist who has seen these problems before and can quickly identify the causes of downtime (even when they're not obvious).
- Telephone+8613256674591
- Email[email protected]
- WhatsApp+8613256674591
- WeChat13256674591
- AddressC623, Jiahui Global Plaza, No. 548, Beiyuan Street, Tianqiao District, Jinan City, Shandong Province
- Factory AddressADD -300m North of Zhangxia Industrial Park, Binhe Road, Zhangxia Town, Changqing District, Jinan